Following long experience with MULTI-MASTER milling heads, ISCAR is expanding their application range by increasing the depth of cut vs. tool diameter ratio from the current 0.7xD to 1.5xD. The new milling heads have been designed for shoulder roughing, semi-finishing and finishing applications with ramping down capability. The new milling heads are available in .312-1.00” diameter range. MM EC-CF-Z7/9-1.5xD Interchangeable 7-9 flute solid carbide endmill heads with 1.5xD flute lengths, different helix, variable pitch and various corner radii. MM EC-CF-Z4-1.5xD Interchangeable solid carbide heads with variable pitch and 1.5xD flute lengths for chatter free roughing and finishing operations. High material removal rates. MM ERS-1.5xD Interchangeable solid carbide rough milling heads with 1.5xD flute lengths, for high metal removal application. It is recommended to use the new long flute milling heads with MM S-A (straight shanks) reinforced, Weldon type or SURELOCK shanks with pull-out prevention helical grooves.
MM EC-CF-Z4-1.5xD Interchangeable Solid Carbide Endmill Heads with 1.5xD Flute Lengths for Chatter Free Roughing and Finishing Carbide Inserts Milling Cutter
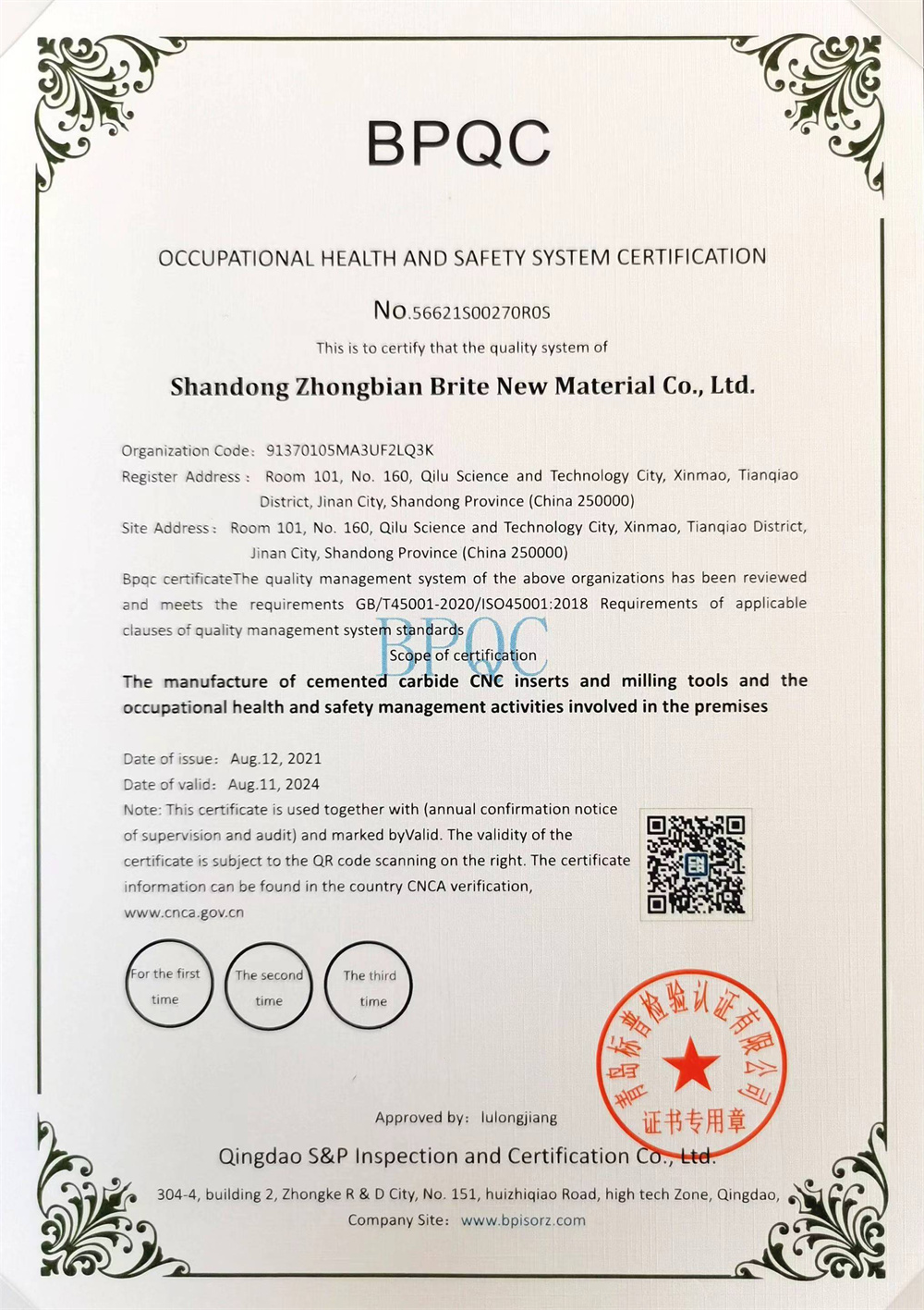
• Do not apply lubricant to the threaded connection. (1) Number of flutes • Maximum depth of cut (APMX) while milling full slot from solid material is 1×DC • Maximum width of cut for milling shoulder with APMX=1.5×DC is 0.3×DC • Reinforced Weldon or SURELOCK shanks (with Safe-Lock® by Haimer pull-out prevention helical grooves) is strongly recommended • In cases of unfavorable machining conditions, the cutting data should be decreased by 20-30%
MM EC-CF-Z7/9-1.5xD Interchangeable 7, 9 Flute Solid Carbide Endmill Heads 36° Helix with 1.5xD Flute Lengths
• Do not apply lubricant to the threaded connection. (1) Number of flutes (2) Maximum ramping angle • Intended for high-speed trochoidal milling and finishing operations with max. width of cut =0.1×DC • Reinforced Weldon or SURELOCK shanks (with Safe-Lock® by Haimer pull-out prevention helical grooves) is strongly recommended • In cases of unfavorable machining conditions, the cutting data should be decreased by 20-30%
MM ERS-1.5xD Interchangeable Solid Carbide Rough Milling Heads with 1.5xD Flute Lengths for High Metal Removal Rates
• Do not apply lubricant to the threaded connection. (1) Number of flutes (2) Maximum ramping angle • Maximum depth of cut (APMX) while milling full slot from solid material is 1×DC • Maximum width of cut for milling shoulder with APMX=1.5×DC is 0.3×DC • Reinforced Weldon or SURELOCK shanks (with Safe-Lock® by Haimer pull-out prevention helical grooves) is strongly recommended • In cases of unfavorable machining conditions, the cutting data should be decreased by 20-30%
Condition of vibration involving the machine, workpiece and cutting tool. Once this condition arises, it is often self-sustaining until the problem is corrected. Chatter can be identified when lines or grooves appear at regular intervals in the workpiece. These lines or grooves are caused by the teeth of the cutter as they vibrate in and out of the workpiece and their spacing depends on the frequency of vibration.
Distance between the bottom of the cut and the uncut surface of the workpiece, measured in a direction at right angles to the machined surface of the workpiece.
Milling cutter held by its shank that cuts on its periphery and, if so configured, on its free end. Takes a variety of shapes (single- and double-end, roughing, ballnose and cup-end) and sizes (stub, medium, long and extra-long). Also comes with differing numbers of flutes.
Grooves and spaces in the body of a tool that permit chip removal from, and cutting-fluid application to, the point of cut.
Machining with several cutters mounted on a single arbor, generally for simultaneous cutting.
Machining operation in which metal or other material is removed by applying power to a rotating cutter. In vertical milling, the cutting tool is mounted vertically on the spindle. In horizontal milling, the cutting tool is mounted horizontally, either directly on the spindle or on an arbor. Horizontal milling is further broken down into conventional milling, where the cutter rotates opposite the direction of feed, or “up” into the workpiece; and climb milling, where the cutter rotates in the direction of feed, or “down” into the workpiece. Milling operations include plane or surface milling, endmilling, facemilling, angle milling, form milling and profiling.
1. On a saw blade, the number of teeth per inch. 2. In threading, the number of threads per inch.
Width of the milled surface, reflecting a face milling cutter’s radial engagement, and a peripheral milling cutter’s axial engagement, in the cut.
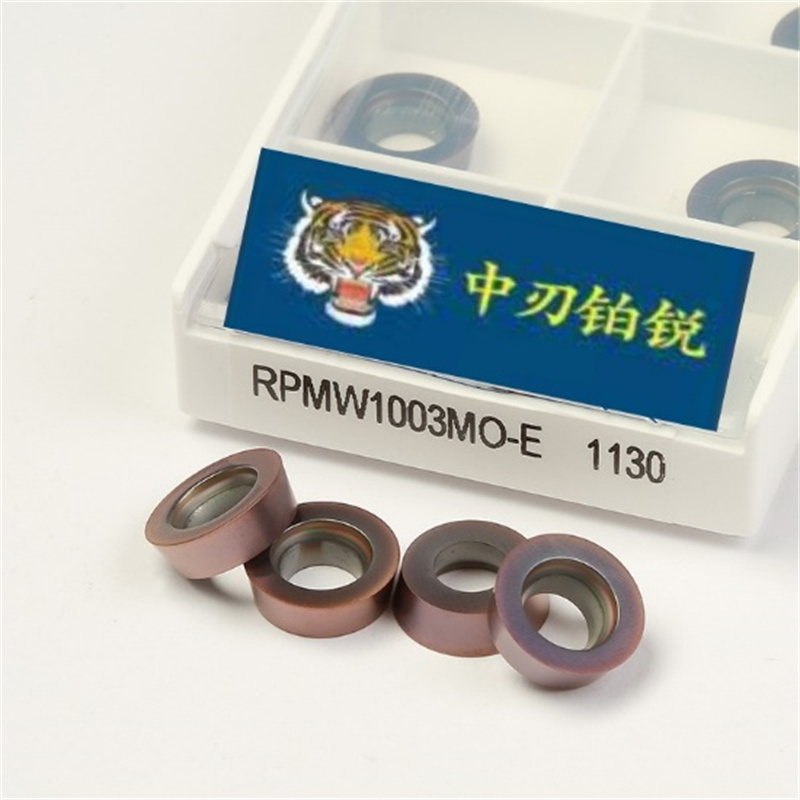
Wnmg Insert Specification © Copyright 1995 - 2024. Cutting Tool Engineering. All rights reserved.